Protecting our people is of the highest importance to us. Everything we do begins with a commitment to safety. The responsibility of safety is solidly placed within the line organization, from the top manager down to the first-line leader.
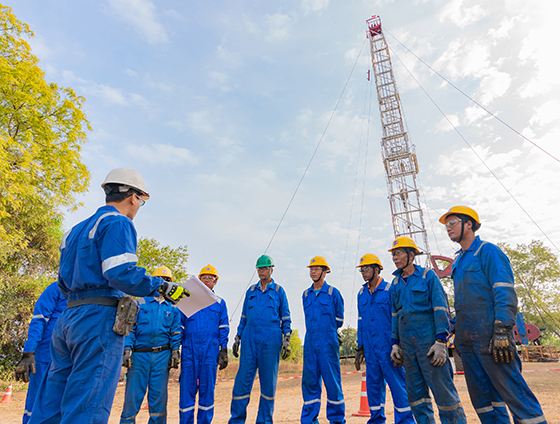
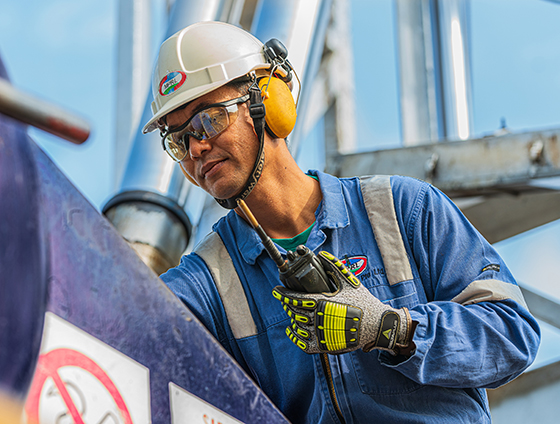
The safety culture of an organization is the product of individual and group values, attitudes, perceptions, competencies, and patterns of behaviour that determine the commitment to, and the style and proficiency of, an organization’s health and safety management. Organization with a positive safety culture are characterized by communications founded on mutual trust, by shared perceptions of the importance of safety and by confidence in the efficacy of preventive measures
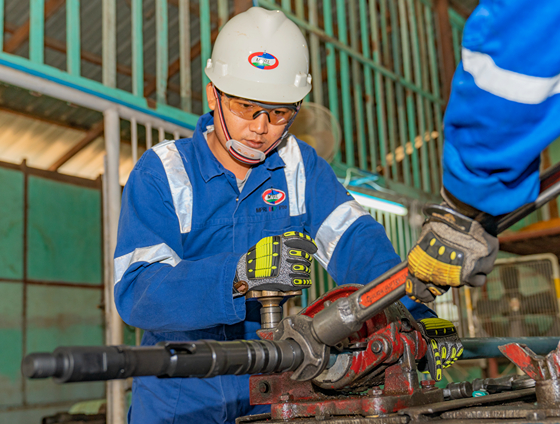
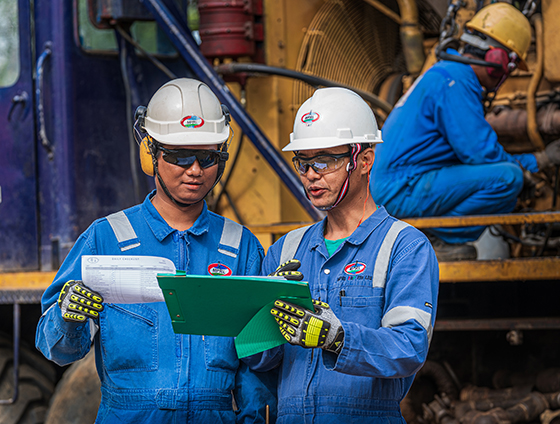
MPRL E&P is committed to continuously improving our Occupational Health & Safety (OHS) performance. In addition, we strive to embed a “Safety First” culture consistent with our fundamental goals, which include:
- Zero Work-related Incidents
- No Harm to People
- Compliance with All Applicable OHS Legislation and Regulations
Our Strategy
- All accidents are preventable.
- No activity is so important that it cannot be done safely.
- OHS performance depends on all employees and contractor personnel working with MPRL E&P. Everyone is responsible for working safely.
- Conduct appropriate trainings to ensure all of our personnel are competent in their respective jobs and understand and adhere to this policy.
- Anyone involved in our business activities may intervene and stop operations (Stop Work Authority) in case they believe that there is an unsafe condition or unsafe action.
- Potential hazards will be identified for all operational activities, and equipment, facilities, and standard operating procedures (SOPs) will be designed with the aim of eliminating accidents and preventing occupational illnesses.
- Industry best practices, procedures, and standards will be established or adopted so as to create a safe and healthy working environment for all workers, contractors, local communities, and other external stakeholders in assets where we operate.
- Arrange for recognized medical professionals to perform medical check-ups for employees or contracted workers as and when required.
- OHS competencies and qualifications shall be taken into consideration in the evaluation process for internal promotions.
- Rectify and report all actions and conditions which could result in an accident/ incident in order to continuously mitigate risks of injury and occupational illness.
- Ensure business plans and individual performance objectives include measurable OHS targets, which are reviewed regularly and updated annually.
- MPRL E&P shall benchmark the company’s H&S performance with that of similar businesses within the oil and gas industry on an annual basis to continuously improve our OHS management.
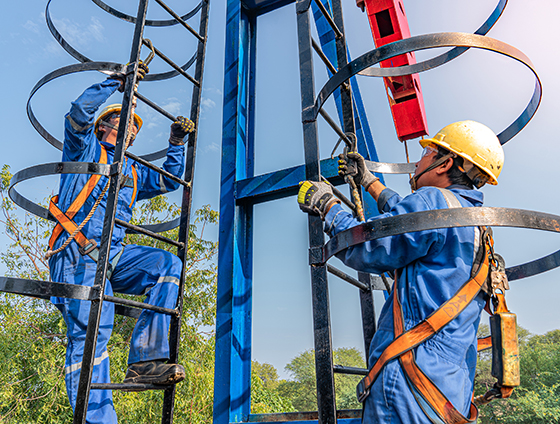
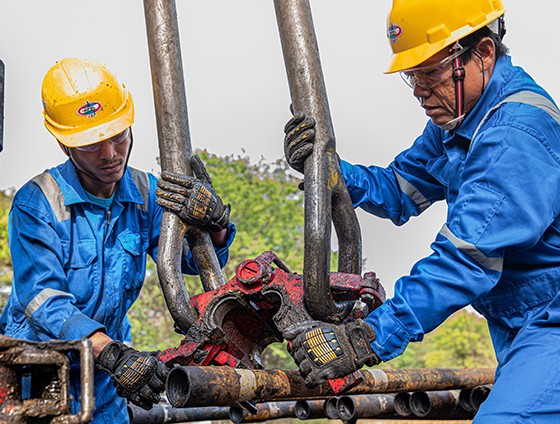
Our Management Framework
To create a safer working environment, MPRL E&P has a core management system that integrates existing and potential project activities. The structure and content of this system is based upon the guidelines of OHSAS 18001:2007 and HSE 65 Managing for Health and Safety.
MPRL E&P HSE Management System

Fig 1: 1 MPRL E&P HSE Management System
In order to expand the existing internal HSE practices, the following processes have been incorporated as a standard requirement of MPRL E&P’s corporate culture: Accessibility to safety cards promoting concern, action, reinforcement, and encouragement (CARE Cards)
- Safety awards
- Pre-job safety meeting
- Daily toolbox talks
- Job safety analysis & risk assessment implementation
- Permit to work system/lockout & tagout/confined space entry
- Weekly safety meetings
- Monthly management meetings
- Monthly HSE committee meetings
- Emergency drill exercises
- HSE promotion
- Safety alerts
- Safety trainings
Together with these activities, MPRL E&P has implemented specific procedures such as a) hazard identification and risk assessment procedures, b) incident investigation and reporting procedures, c) transportation management procedures, and d) lifting operation procedures.
Additionally, these practices and procedures have been extended into our supply chain and provide instructions on the monitoring and management of contractors’ practices, where required, in order to ensure that they meet the HSE standards stipulated by MPRL E&P.
HSE department has several roles in dealing with company workforces, assets and properties, procedures and standards compliant. Main functions of the department comprises as follows:
- Generating daily, weekly and monthly HSE reports to management
- Designing HSE training program and delivering series of training to the workforce as per planned schedule in order to raise the awareness level of the employees
- Liaising with Human Resources Department to ensure the adequacy of competency level of each position in the organization
- Facilitating to the technical team members in hazard identification and risk assessments on the operations and ensuring they kept reviewed and updated on regular basis.
- Ensuring that planned preventive maintenance program in place and implementing for operational assets to achieve minimal downtime in operation as well as to prevent accidents which might be caused by the failure of the assets.
- Developing positive safety culture in the organization by creating programs such as behavioural change program as the human error is the most common cause of accident by its nature.
- Monitoring and recording incident statistics and comparing it to the previous year’s data to find the weakness or the areas for future improvement.
- Benchmarking the company’s incident statistic with the similar industries to identify where we are and where we need to be.
- Conducting incident investigation once the accident or near miss occurred in order to identify the root causes of each event so that similar occurrences will be prevented.
- Circulating safety alerts is also a part of departmental role to keep everybody vigilant.
HSE department mainly focus on the workers’ participation in HSE programs and by doing so, opportunities are opened up to everyone to raise their concerns without barriers with the mind set of “I am responsible for Health, Safety and Environment of my colleagues”